A Day in the Sheep Shearing Sheds in Australia: What it’s Really Like
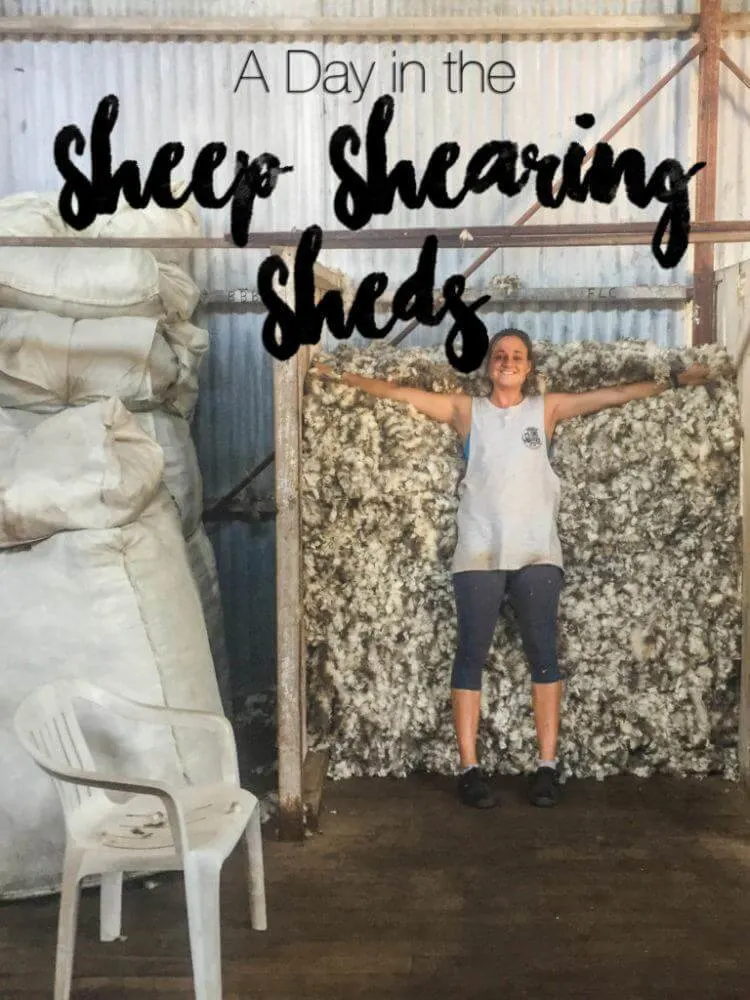
While I was living and working out in the middle of country Australia, I spent my day off visiting the Australian sheep shearing sheds. I had no idea what to expect, but helping the shearers and roustabouts with their duties and seeing how the whole sheep shearing process works is one of my favorite and most interesting Australian country stories.
With the music thumping and the shears buzzing, I readied myself for the next fleece to be thrown out across the wool table. With the other roustabouts, I picked out all the gross bits from the sheep’s wool- any sweat stains, blood, accidental skin, or poop, and separated wool from different parts of the body as well – the belly, legs, and head wool – and threw the pieces into their respective bins as quickly as possible because there were more fleeces ready to be done.
Do you ever just pause and take a step back from what you are doing and think…. “Wait a minute… How did I get here? What am I doing?”
I had quite a few moments like this when I went out to the sheep shearing sheds on my day off to experience a day of sheep shearing (apparently one of the most iconic activities in rural Australia!). Because this concept was as foreign to me when I got out here to the Australian bush/country as it is to many of you reading, I’ll start at the beginning!
Sheep Shearing in Australia: A Day in the Life
So nearly all the farms out here where I am in WA farm two things – sheep and grain. A single farm usually has at least a few thousand sheep, and around here they are mostly farmed for their wool (or meat). This means that once a year, all 2-3+ thousand sheep must be sheared of their thick coats, which are taken, sorted, and shipped all over the place for many different uses.
Each sheep farmer usually has their own sheep shearing shed, which is all set up with four shearing stands. The sheep shearing sheds have all sorts of passageways and compartments outside for the sheep to be shuffled into in groups, as the dogs and farmers move them into and out of the shed.
Subscribe to Adventures & Sunsets!
Each month I send out an update with the month’s most fascinating content, best travel deals and products, fun facts, best photos, and where we’ve been. Join me!OKAY I’M IN!I consent to receiving emails and personalized ads.
When it’s that time of the year, a sheep shearing team is hired to come out and complete the extremely tough and physical job of shearing the wool off of the hundreds of sheep. A sheep shearing team is comprised of 8 people usually – four shearers and four roustabouts, who gather, pick, class, and press the wool after it has been sheared from the sheep. This is what I did when I went out for the day; I learned from and helped out the ‘rouseys’ as they are called.
I had to sit and take it all in for a little while before jumping in – it really is an insanely fast-paced profession. The sheep shearers arrive at the shed at 7am, chuck an iPod into some pretty loud speakers, and are full speed ahead by 730am. They do four two hour sessions with breaks in between. The shearers hook up their high-tech sheep shears (I think thats what they’re called – kind of like a fancy and extra sharp version of buzz cutters for hair 😛 ) and grab a sheep by its front legs from a mob that has already been herded intoone compartment of the the sheep shearing shed, and very specifically and expertly shear the wool off of it in a way that the entire fleece comes off as one, like peeling off a jacket that’s still in the shape of the sheep.
The Process of Sheep Shearing – As I Understand It
They shear the sheep with an expensive pair of these! Shearers must have their own equipment.
They shear the belly first because the wool is a bit finer, and that is put into a specific bucket for a specific function. They then do the head and front legs, and continue in order until they are done with the sheep. This is where the rouseys come in – they come and collect the finished fleece, bundle it up by grabbing the back legs and rolling it up super specifically to the front legs, and then they throw it out over a wool table so it lands insanely perfectly in the form of the actual sheep. (I tried this a few times and failed miserably…. but I got better as I went on!)
Then the other rouseys (they are all assigned to specific roles as the day goes on – picking up the wool, picking it, classing it, pressing it, sweeping excess wool up, and moving sheep up into the shed) pick out all the ‘bad’ bits out of the wool. Now I’m sure you can picture a sheep living out on a farm, eating and walking through paddocks, pooping and peeing and sweating and all of the above. When the sheep does those things with a thick fur coat on…. things get in it’s coat. When you shear off that fur coat… there is still a bunch of crap in it. And when you make a t-shirt or a bath mat or a pair of socks out of wool, well, you don’t want poop in it. So it has to be picked out. Which is the ever-so-lovely, not-gross-at-all roustabout shearing duties! Thankfully, they get paid very well!
So once the fleece gets thrown out across the table, the other rouseys come and help pick it. Somehow when sheep sweat, it culminates into this thick, greasy, brown mat in their fur, which you must pick out and throw into a bin of what they call ‘pieces.’ (I thought this was poop for the first long while so at least grease is better than actual shit, right?!) If there is any stray poop or pee, that must be thrown into the same bin. When you find the wool bit from its cheek and head, it goes in a certain bin as well (it is softer and more valuable). The wool from its legs/feet must go into a certain bin too because there are medullated fibers that grow on their legs that apparently don’t take well to dye, so must be separated from the good wool.
Also, as the sheep shearers must move very quickly (they each do over 150 sheep in an 8 hour day, and get paid per sheep), sometimes they accidentally knick the skin of the sheep… sometimes a bit more than a knick, unfortunately (and sheep have very wrinkly skin!). So the rouseys must also put wool with any blood or actual shaves of skin on it, in a bin to sort out as well. Later, someone gets the lovely job of cutting the skin bits off and putting the wool back in the pile!
One of the rouseys expertly throwing the fleece out across the table.What a little bit of skin looks like in the woolWhat a big piece of skin looks like in the wool. Eek!
The wool press (right) presses the wool down into these white packages (left!)
When the wool is finished being sorted out (which usually takes like a single minute because there are fleeces from all 4 shearers coming in at all times) The wool is collected and classed by one of the head rouseys, who decides on the quality of the wool (usually the length and strength) and puts it in its respective pile. Then, the presser helps put it into a big press they have in all shearing sheds – a big machine that you fashion with a big white tarp, and the wool gets pressed down into it until you fasten it up all ready to be sent out to wool shops!
The wool shops clean the wool again (because the job here is done so quickly it couldn’t be perfect) and then they are the ones to send it out to more specific places where the wool can be used for shirts, sweaters, socks, hats, carpets, floor mats, and even insulation for houses! Crazy, huh? On one of my days in the pub, one of the farmers commented that my sweater was probably made of wool… we looked at the tag, and it was! That was a weird realization to make that a shirt I don’t even think about wearing started by being sheered off of a little sheep somewhere in remote farmland 😛
The poor little freshly sheared, naked-looking sheep…. and the ones in the back about to go in!
There are also different ages of sheep to shear, and they usually do them in sections of male, female, and age. We started off with the ewes, and then did the teenaged sheep, and then the baby lambs, whose fleeces were almost laughably smaller and much easier to deal with.
While I was out there, I of course had to try shearing a sheep myself! One of the shearers let me try the end of his last sheep before lunch. He first tried to teach me how to position the poor bugger, holding its head between your legs facing forward with one leg on each side so it couldn’t kick. It was damn heavy and I couldn’t really get the positioning right but he gave me the shears anyway…
The shears vibrate so hard they are almost hard to hold onto! The sheep had a few bleeding cuts from when the shearer was working (which got all over my shoe and shirt), but when I tried I didn’t cut the wool even near close enough to the skin… I was too afraid to cut the poor sheep! I had to go over the same spots a few times to get it short enough, and tried a bit of its leg and finished as much as I could before the sheep shearer had to clean the rest of it up for me. Ha, I was pretty bad and it was pretty laughable really, but gives you so much respect for them doing it all day!
So anyway, at first all of this must sound really, well, dirty. And that’s what I thought when I first tried helping the rouseys. At first sheep shearing left me pretty grossed out and I didn’t last very long. Plus, they are all so zoned-in and good at it that I felt a little lost and not helpful. But once I pushed past this zone of uncomfortableness, I grew to weirdly, strangely, almost even enjoy doing it.
I know, right?! How is that possible? Coming from the way I just explained everything, sheep shearing kind of sounds like the last thing a girl from the Californian suburbs would want to be doing. But in all honesty you really get past the grossness of it and get used to it. Now, I wouldn’t go touching my face or anything, but I found that I enjoyed the fast pace of the work and how active it was.
This was such a contrast coming from a Monday night in the pub where I sat behind the bar for over 2 hours waiting for the last 2 old men to finish their conversation about farming and leave, bored out of my mind. I had already stocked the whole coolroom, replied to all my instagram comments, wiped the bar down, and did basically everything productive I could think of, and was just about ready to dive into the wall.
Fastforward 12 hours and I was in the middle of that loud music, picking bits of wool and watching extremely skilled workers in a field I never even knew existed, learning more than I ever could if I was just traveling. The fast pace of sheep shearing was great and I loved the fact that you can just get into a zone and just do your thing. I gazed out into the golden fields of grain – probably barley or wheat – that was just about ready to be harvested, with bushland in the background, some silos in the foreground, and a warm summer breeze coming through the sheep shearing shed. I saw the farmer and his sheepdog expertly herding the next round of sheep around the corner into the paddock, with the dog expertly taming the herd almost on its own.
This made me think to myself that this is an experience you can’t get just traveling. It’t not like you can sign up for a tour and they will take you to see some sheep shearing or farming. This is a direct outcome of actually living somewhere, placing yourself directly into another culture and getting out to experience it. This is one of the reasons I enjoy living in different places a lot rather than just traveling through; there are some experiences you just can’t get any other way.
And as soon as I finished this thought, the head rousey snapped me back into reality. “Got three fleeces ready here!” she said as she swept some stray wool back under the table with their special plastic brooms. I gathered a fleece from the ground and catapulted it across the wool table, and honestly impressed myself a bit with how much I had improved! And then I was right back into it.
At the end of the day, I got to enjoy a beer (or four) with the whole sheep shearing team, having completed pretty much a whole day with them. Beer has never tasted so good after a long, hard day’s work! So much respect for these people!